Some industries require highly reliable modern electronics like PCBs and steps must be taken to ensure the optimal performance of these parts.
When talking specifically about aerospace and automotive PCBs, among the several factors that influence PCB performance is plating, which must be reliable. Here, we will discuss the technical reasons why reliable plating is essential for PCBs in the automotive and aerospace industries.
The Role Of Plating In PCBs
Plating in PCBs involves the deposition of a metallic layer over the copper circuitry and this is done to achieve several objectives. These include:
- Enhancing Conductivity: High-quality plating ensures low resistance pathways for electrical signals. This is useful in high-speed data and power transmission.ย
- Corrosion Protection: Plating acts as a barrier against oxidation and chemical reactions that degrade the copper substrate.ย
- Surface Preparation for Soldering: When attaching other components to the circuit board, reliable plating will create a smooth, solderable surface for the attachment.ย
- Wear and Tear Resistance: For harsh environments like those of the automotive and aerospace industries, the PCBs must have mechanical strength that can help them withstand such conditions. This is achieved by using durable plating materials.ย
Industry Specific Challenges
Automotive Requirements
Automotive PCBs will generally operate in environments with extreme temperature variations, high humidity, and exposure to chemicals such as fuel and lubricants. Since these high-tech PCBs are used in critical systems like advanced driver assistance systems, engine control units, and more, reliable plating in these systems will ensure a few things:
- Thermal stability: The plating makes the PCBs resistant to thermal cycling, where repeated heating and cooling can cause material fatigue.
- Corrosion Resistance: It will protect the PCB against moisture and salt, particularly in external vehicle sensors and marine applications.ย
- Vibration Durability: Plated PCBs have better mechanical stability under constant vibrations and shocks.
Aerospace Demands
Aerospace PCBs will be subjected to even harsher conditions from extreme temperatures to high radiation levels since they are used in applications like avionics, satellite systems, and the military PCBs used in unmanned aerial vehicles. Here are some plating requirements that are considered:
- Vacuum Compatibility: Plating PCBs to prevent outgassing that could compromise electronic functionality in space environments.
- Radiation Hardening: Using plating materials that resist ionizing radiation and mitigate signal degradation.ย
- Electromagnetic Compatibility: This is required to maintain signal integrity in environments with high electromagnetic interference.ย
As you can see, both industries require reliable plating, to perform significantly important tasks in their respective fields. But what happens if the plating is unreliable?
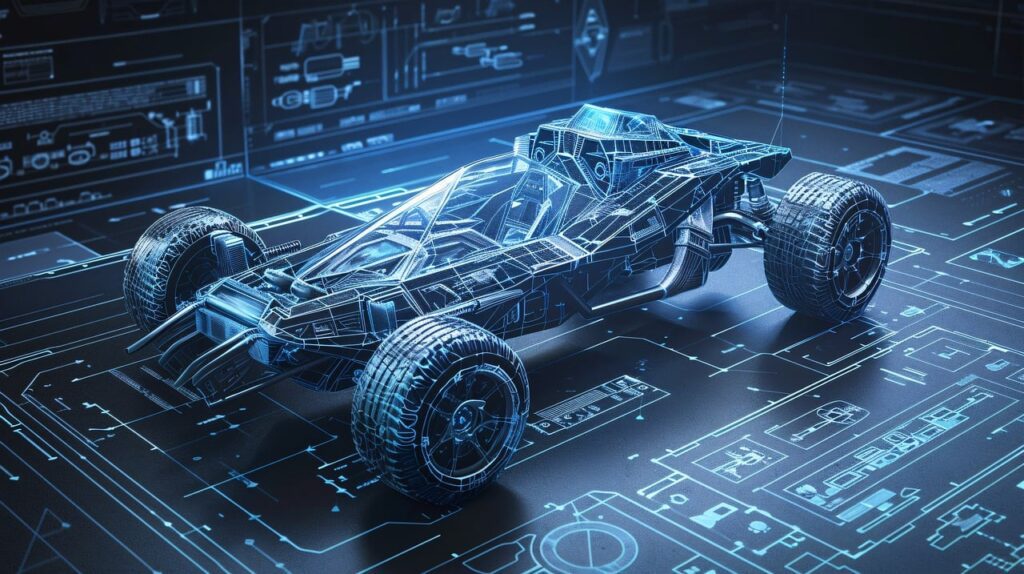
Challenges Of Unreliable Plating
Unreliable plating includes several issues like defects or inconsistencies in the plating process, material selection, and more. For the aerospace and automotive PCBs, this is a serious problem because it often leads to a cascade of failures.
Letโs discuss some of the challenges and their impacts:
Microcracks in Plated Vias and Pads
Microcracks will often result from insufficient plating thickness, poor adhesion, or thermal stress during operation.
These cracks interrupt electrical signals between PCB layers in critical systems like avionics and engine control units.
Without reliable plating, automotive systems, especially EVs, get cracked vias in power circuits that can lead to overheating or energy loss, reducing system efficiency and reliability.
Voids in Plated Layers
If via walls are improperly cleaned, the surface is not sufficiently activated before plating, or there is poor control during the plating process, voids will occur.
Their occurrence in aerospace PCBs increases resistance which leads to signal integrity issues and a possibility of short circuits during rapid thermal cycling at high altitudes.
For automotive PCBs, voids can cause localized overheating, particularly in high-current paths, jeopardizing power delivery in systems like ADAS or battery management systems.
Other Common Problems Resulting From Unreliable Plating
- Delamination of plating layers
- Oxidation and corrosion
- Uneven plating thickness
- Poor solderability
- Thermal and mechanical stress failures
- Plating material compatibility issues.
How To Get Reliable Plating For Your PCBs
The best way to avoid all the issues that come with unreliable plating is to work with reputable plating professionals who have years of experience and can navigate the challenges of plating that are unique to each project. Youโll find this expertise with Alternate Finishing, Inc. (AFI).
AFI is located in Metro Boston and we serve customers across the USA and Canada with precious metal plating services. As an IPC member, that is AS9100D, ISO 9001:2015, and ITAR registered, our work is reliable and we have a quick turnaround on jobs. If you are looking for reliable plating for your automotive or aerospace PCBs, call us for a quote.